Quality Made Us Global
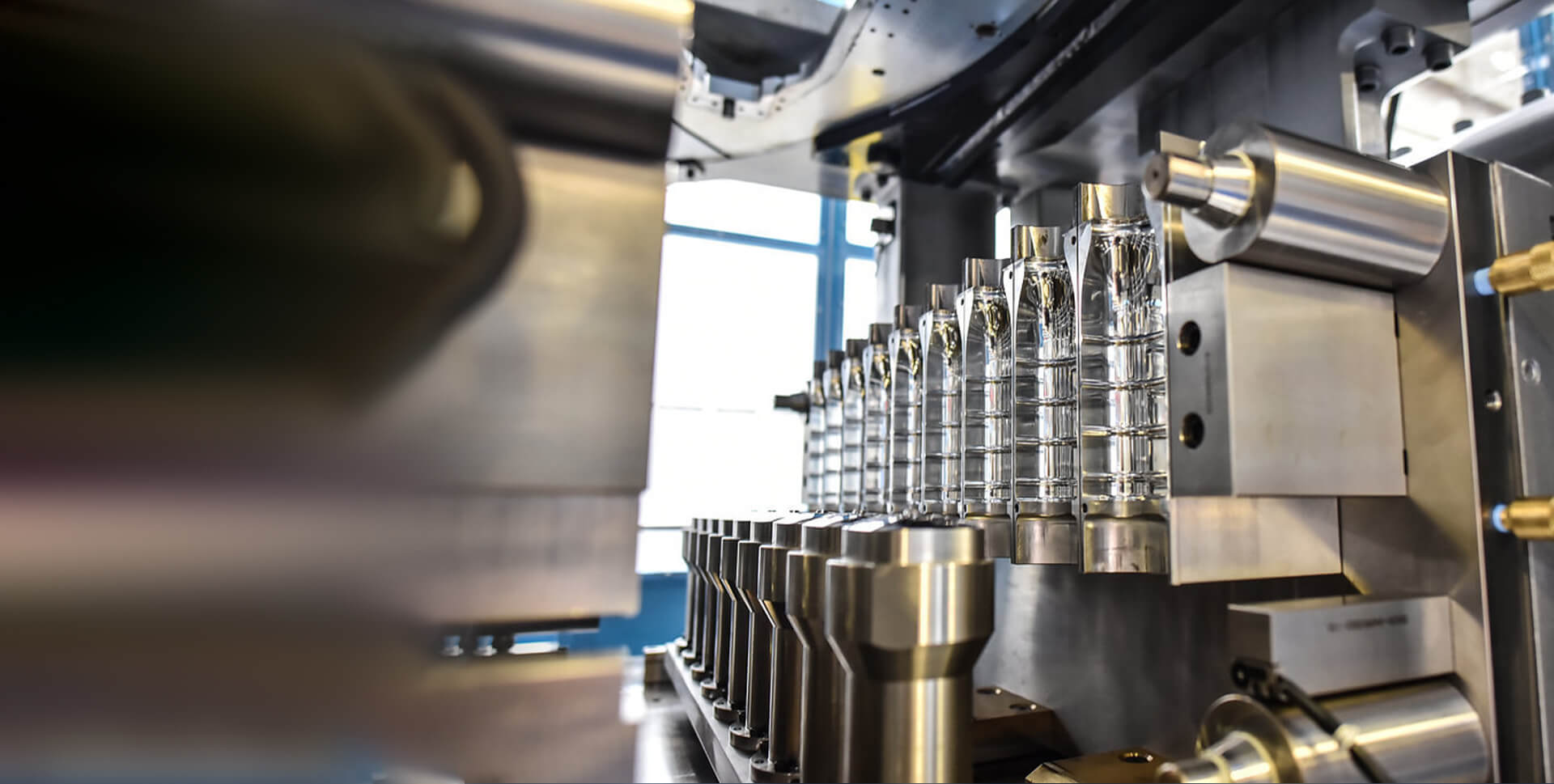
With our fleet of 70+ injection molding machines, an in-house, full-service tooling department, product development and project management expertise, and an unparalleled customer service team, we handle a huge range of plastic injection molding projects for all kinds of companies across multiple industries. Our collaborative partnership approach with every customer has also resulted in the creation of three affiliate companies: Global Forming, Global Packaging, and Global Air. All four companies are served by our warehousing and distribution facility with its 250,000 square feet of carefully managed space.
Tracking the Trends to Better Serve You
Technology and automation continue to be the leading change drivers in the plastic injection molding industry. Smarter equipment, digitization, and ever-increasing quality requirements are areas we watch closely as they advance. When we determine a trend or development will be of benefit for our customers, we waste no time to incorporate it into our practices or our facility if it’s new technology or equipment.
Our commitment to continuous improvement means we never “settle” for anything. “Good enough” is never good enough at Global Plastics. We are always in search of the better, smarter, faster way to operate. Throughout our facilities you’ll see hard evidence of continuous improvement and automation, whether robots and co-bots or just investing in continually upgrading our equipment with new models. We have a cross-functional continuous improvement team meeting every week for the sole purpose of discussing areas for improvement.
Customer Service Dedicated to Each Client
Global Plastics has invested heavily in assembling a veteran customer service team. They not only deeply understand our business but also work tirelessly to learn about each customer’s business and its needs. Something that distinguishes our approach to customer service from our competitors is how each of our customer service representatives is dedicated to individual customer accounts. This allows for deeper, more personal, and collaborative relationships. This is a rare occurrence in any industry these days, but our experience has proven it to be a truly essential ingredient to both your success and ours.
Quality Parts Right the First Time—On Time
Our focus on quality does not come at the expense of time. Speed and flexibility are two of our greatest strengths. By having vertically integrated engineering, tooling, and production departments under one roof, we can often outpace our competitors. Change happens, as they say, but our customers appreciate and remember the lengths we will go to in making sure their needs are met—that’s the Global Plastics difference. Get in touch through the contact us page of our website to learn more and get a quote for our services.