Quality Made Us Global
Automotive Injection Molding with Global Plastics
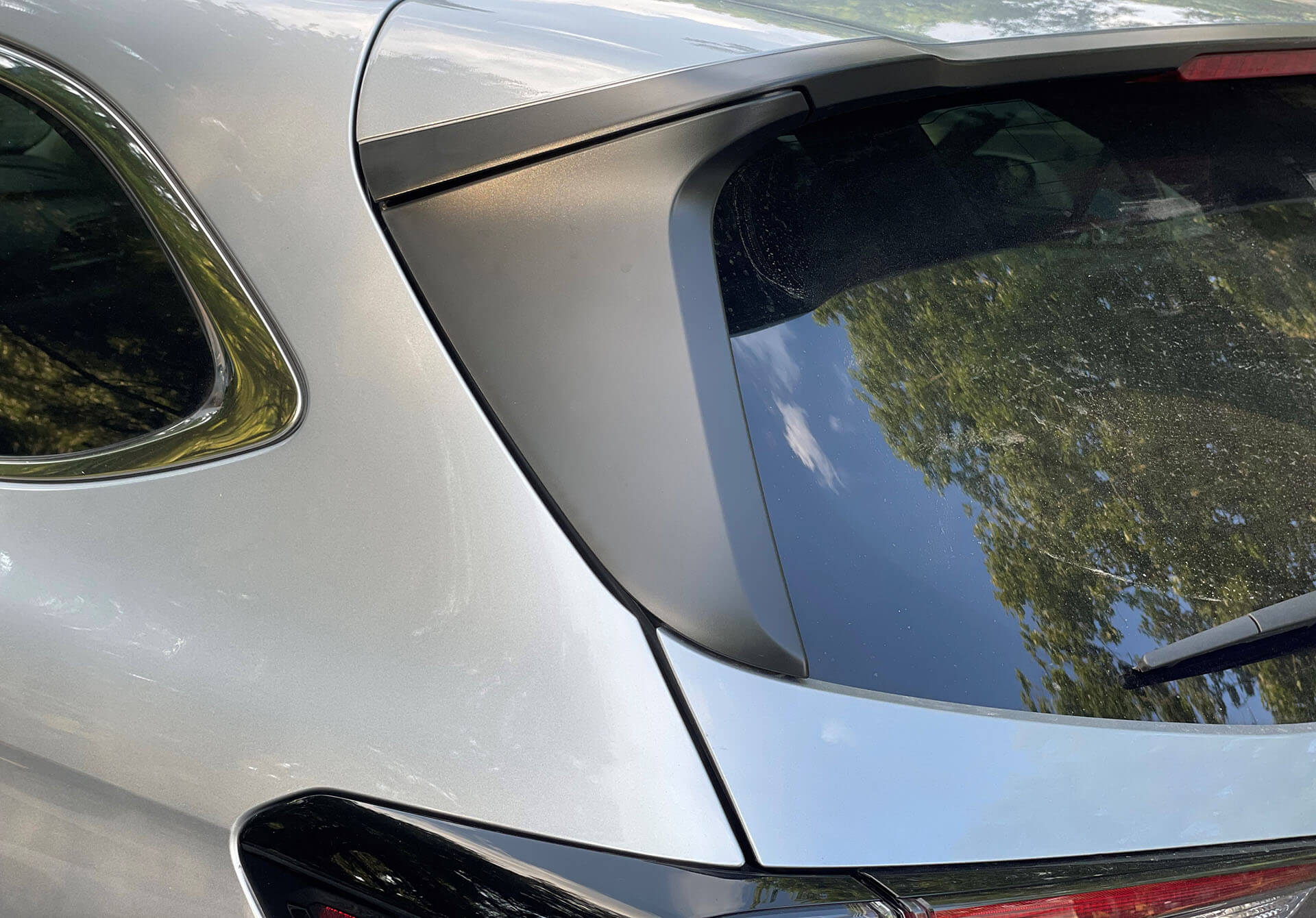
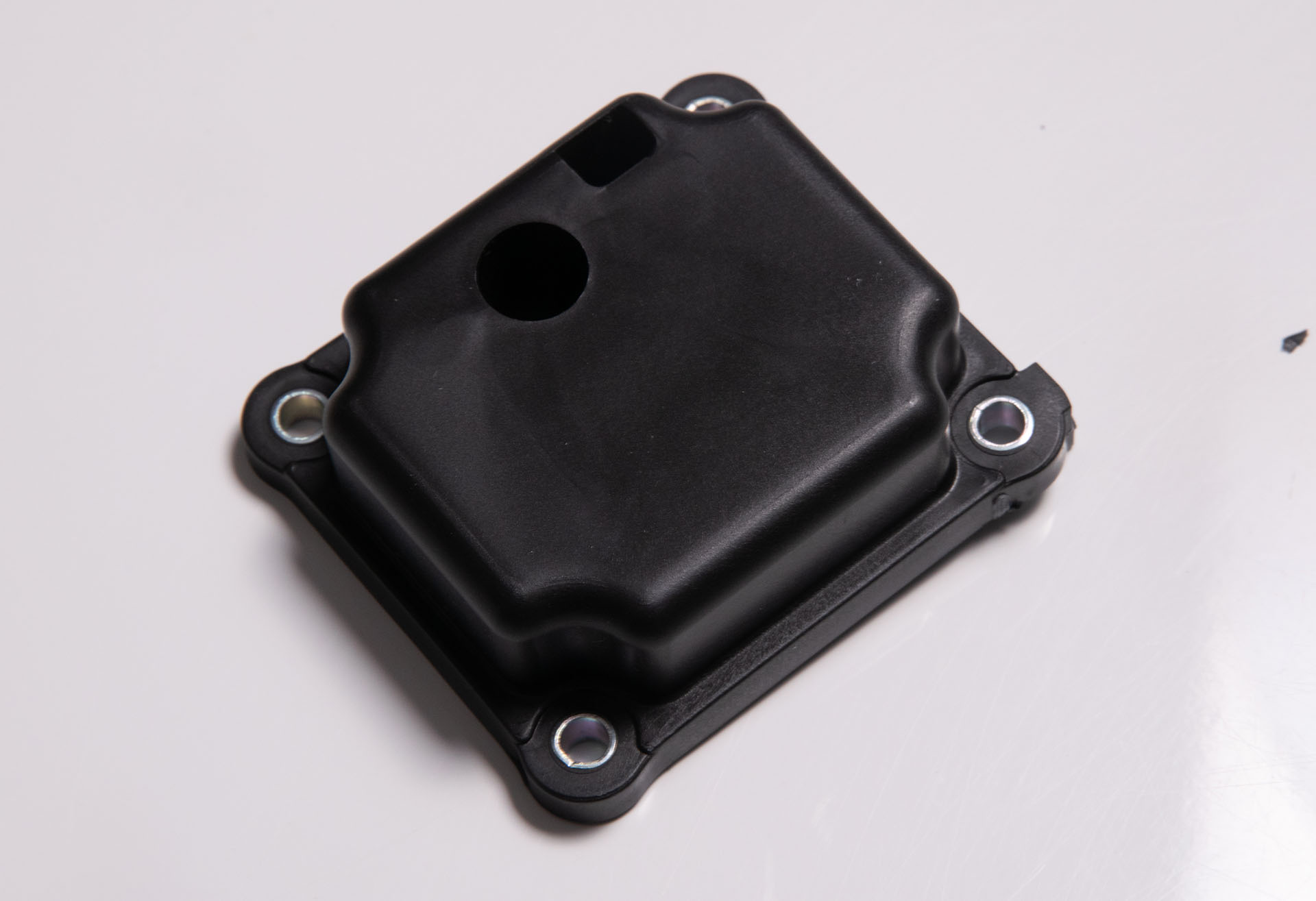
In the automotive industry, plastic components made by the injection molding process have been on the rise in recent decades. As the number and variety of plastic resins has grown, so have the opportunities for converting metal automotive components to plastic. Plastic injection molding solutions can reduce automotive component costs while also achieving lightweighting and right-weighting goals to reduce vehicle weight for greater fuel efficiency.
Global Plastics has extensive experience serving automotive industry clients in ways that reduce risk in their supply chains. We are ISO 9001 and IATF 16949 certified for quality management. Learn more about our automotive injection molding processes in this article, and feel free to get in touch through the contact us page of our website to initiate a quote for our services.
The Rise of Plastic Injection Molded Parts for the Automotive Sector
It’s hard to imagine a car without plastic parts, but there was a time when every vehicle was made nearly entirely from metal, which made automobiles more like tanks. But when plastics began growing rapidly, it wasn’t long before the automotive industry began experimenting with the incorporation of plastic parts into vehicle design and production. Today, the automotive industry relies heavily on injection molding for a wide range of plastic parts used for engine components, exterior components, and interior components.
Global Plastics assists automotive sector clients with injected molded plastic part projects from start to finish, including design, prototyping, mold tooling with our in-house tooling department, and production runs of precision products for the full range of automotive applications. Our experience, our equipment, and our process all work together to achieve superior results within a framework of commitment to excellence in customer service and support.
Quality Injection Molded Plastic Components in the Modern Vehicle
Whether it’s for regular cars, SUVs, pickup trucks, vans, hybrids, or electric vehicles, thermoplastic injection molding can be used in the design and manufacturing of a wide range of plastic products used as components through the modern automobile, including the following:

Under the Hood
Cylinder head covers, oil pans, wiring harnesses and connectors, clips and housings, hoses and tubes, and so on.

Exterior Parts
Light housings, splash guards, bumpers, fenders, grilles, door panels, floor rails, sunroof and moonroof covers, parts for convertible roof assemblies, door handles, door panels, radiators, radiator supports, header and nose panels, mirrors, tailgates and trunk lids, fuel tank caps, and so on.

Interior Components
Instrumentation components, buttons and control levers, bezel panels, radio housings and internal components, interior surfaces, dashboard and console covers and brackets, shifter knobs, cupholder inserts, door handles, glove compartments, air vents and ducts, seat belt components, decorative elements, and so on.
Plastics for Automotive Injection Molding
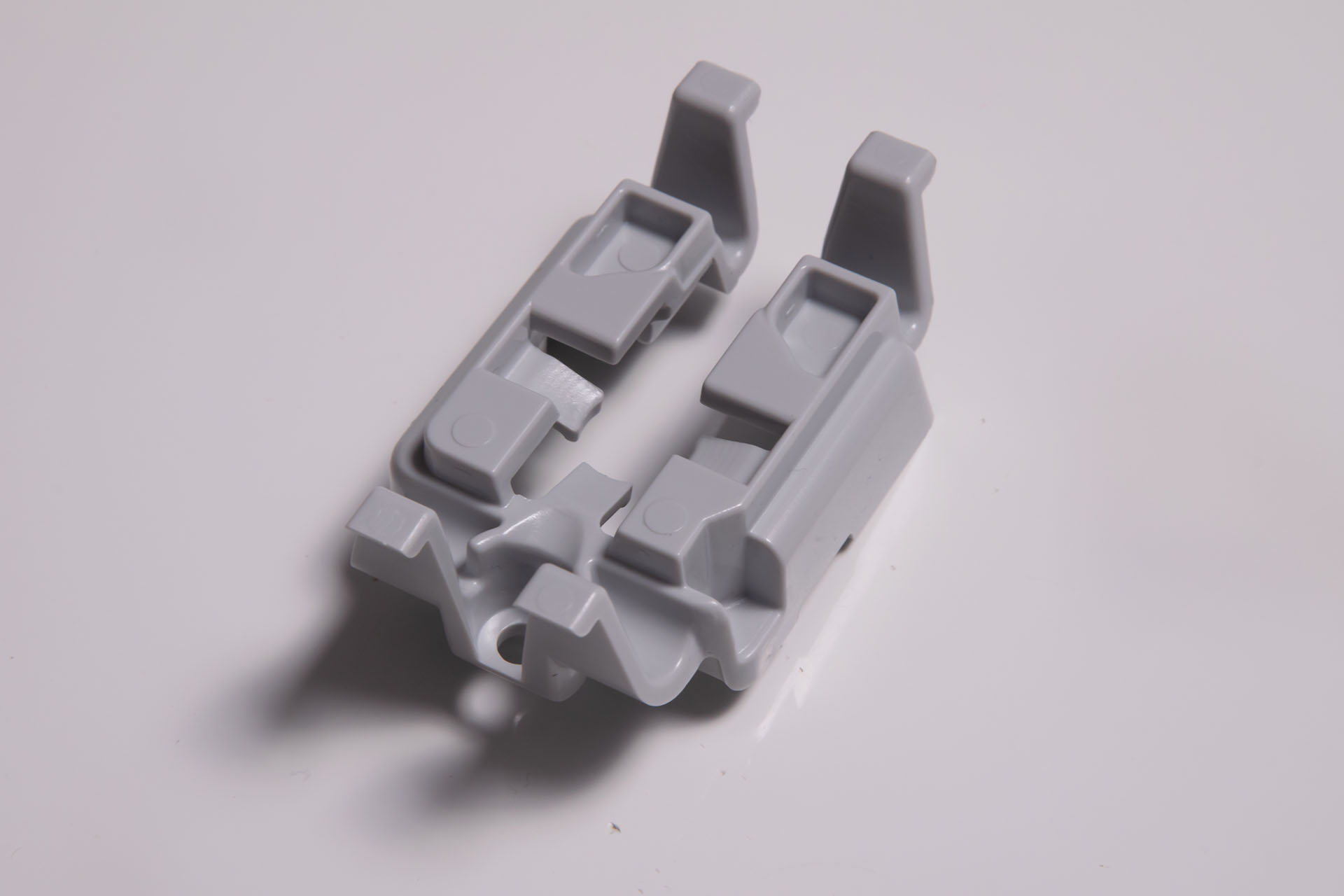
Great care must be taken in the selection of a plastic resin for any part of a vehicle. The specific application will guide polymer selection based on the amount of wear the plastic part will experience, along with other environmental factors and requirements. The good news is that whatever automotive application you’re looking at, there is a plastic resin material that fits the bill, including the following common materials:
- ABS: Acrylonitrile butadiene styrene is known for being strong and rigid, as well as resistant to a variety of bases and acids (although some solvents and chlorinated hydrocarbons can damage it). These characteristics make ABS resin a common choice for vehicle dashboards and covers.
- PA: Polyamide, more commonly known a nylon, is a tough and relatively hard material. Its properties include chemical and abrasion resistance as well as low shrinkage and warp. Nylon plastic resins provide superior wear resistance, and excellent temperature and impact properties. It is often used in making screw grommets, nuts, and rivets, both for interior and exterior applications, among other items.
- PMMA: Polymethyl Methacrylate (acrylic) is stiff, durable, and hard. It is transparent and can be polished to a sheen, which is why it is often used for headlight covers and interior display screens for electronic items such as the radio, navigation system, and so on.
- PP: Polypropylene is lightweight, of moderate hardness/softness and has high chemical resistance to water, acids, bases, and many solvents. It’s often used in high-intensity automobile parts such as bumpers, battery covers, and cable insulation.
- PVC: Polyvinyl Chloride is a tough and durable, strong and rigid material with good chemical resistance to a variety of acids and bases, making it a good choice for cable insulation, dashboards, and interior panels.
- PET: Not just for plastic bottles, Polyethylene terephthalate is in the polyester family and the right formulations of this resin can be used for vehicle body panels. Some automobiles are essentially a PET car with an all-plastic structure on a metal frame. ?
Global Plastics: Your Automotive Injection Molding Services Partner
When you need a reliable plastic component manufacturing solution in the midwestern region of the United States, look no further than the injection molding services of Global Plastics. We have the right technologies (a fleet of more than 75 injection molding machines, along with a full-service tooling department) and decades of experience meeting the needs of automotive industry clients. Get in touch with us through the contact us page of our website to learn more about how Global Plastics can meet your automotive injection molding needs.
Global Plastics has Safe Quality Food (SQF) certification for manufacturing food packaging materials and plastic molded food closures.