Sonic Welding
Quality Made Us Global
Secondary Operations
Bonding Plastic Parts with Ultrasonic Welding
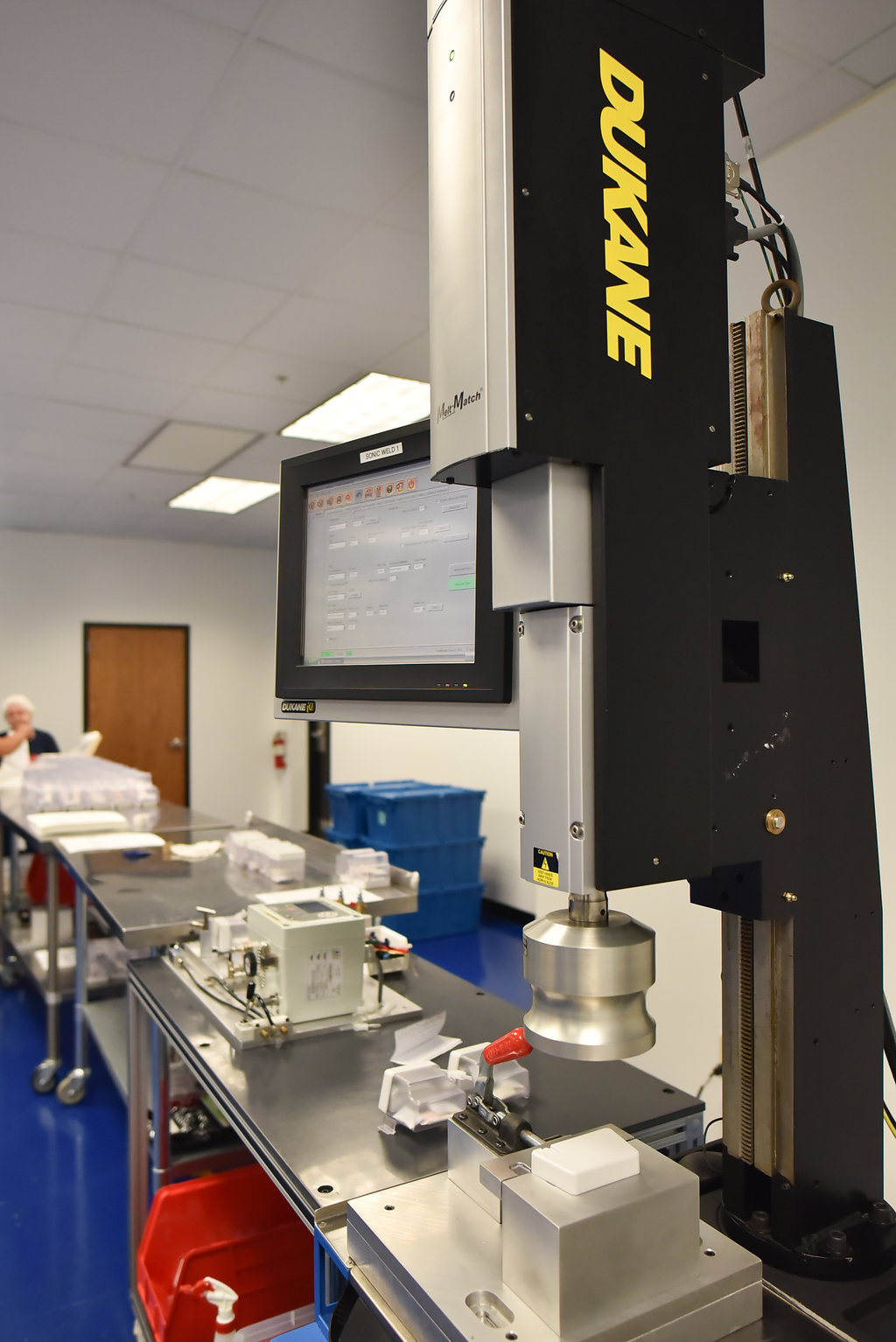
Parameters for Ultrasonic Welding
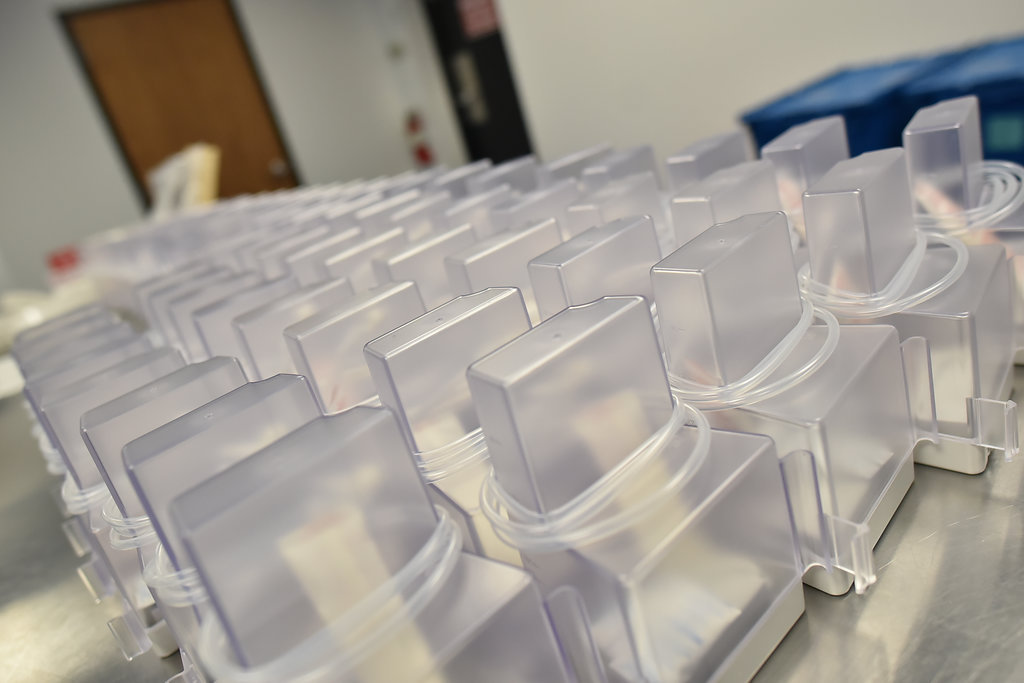
In addition to chemical compatibility, the two thermoplastic materials to be joined must have melting points within 40ºF (6ºC) of each other. They must also be of molecular structure. While similar amorphous polymers have a high probability for being welded together, most semi-crystalline materials are only compatible with themselves.
Additional factors beyond chemical compatibility that can affect weldability include hygroscopicity, mold release agents, lubricants, plasticizers, fillers, flame retardants, regrind, pigments, and resin grades. Global plastics is deeply familiar with all these compatibility and other factors related to ultrasonic welding.
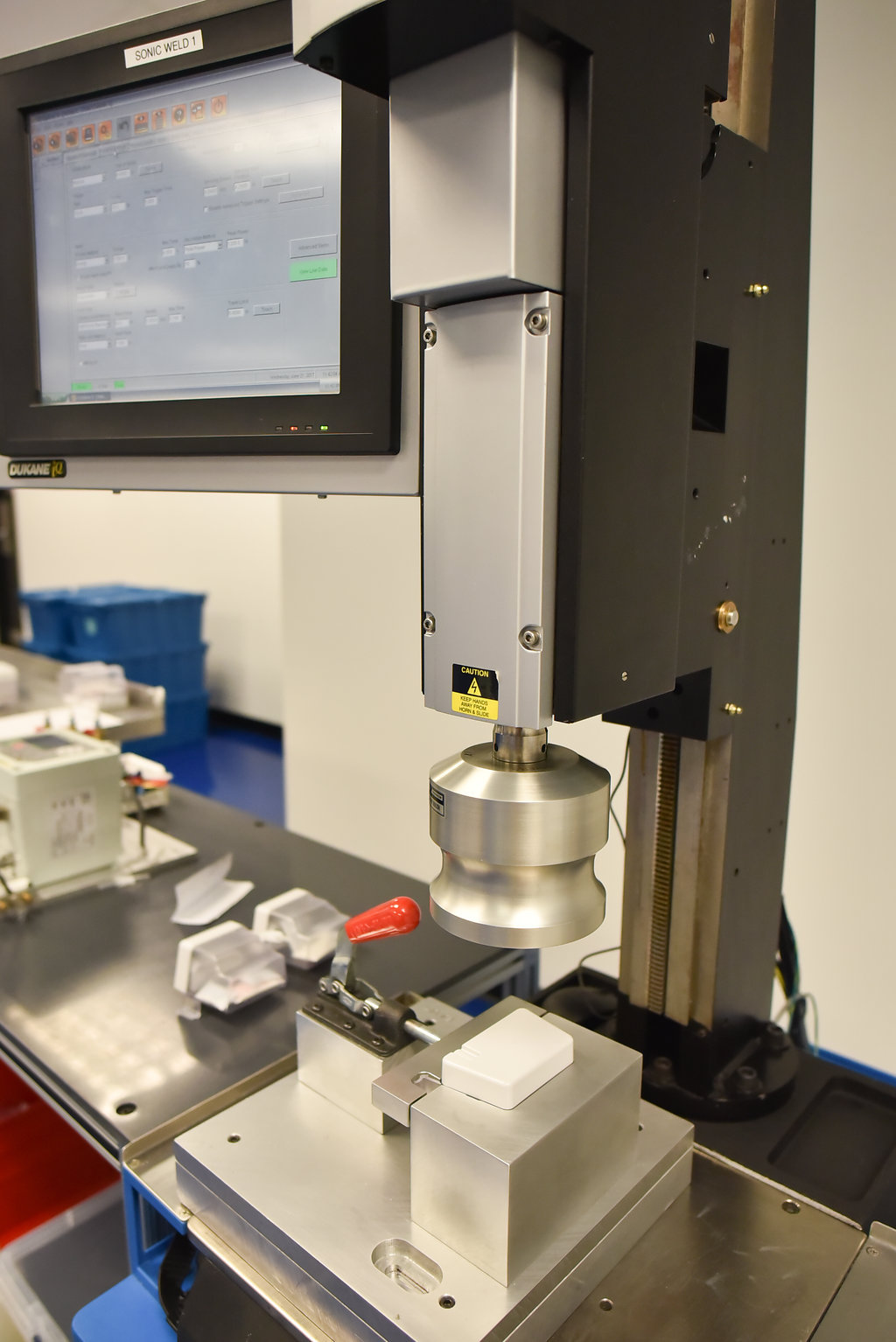
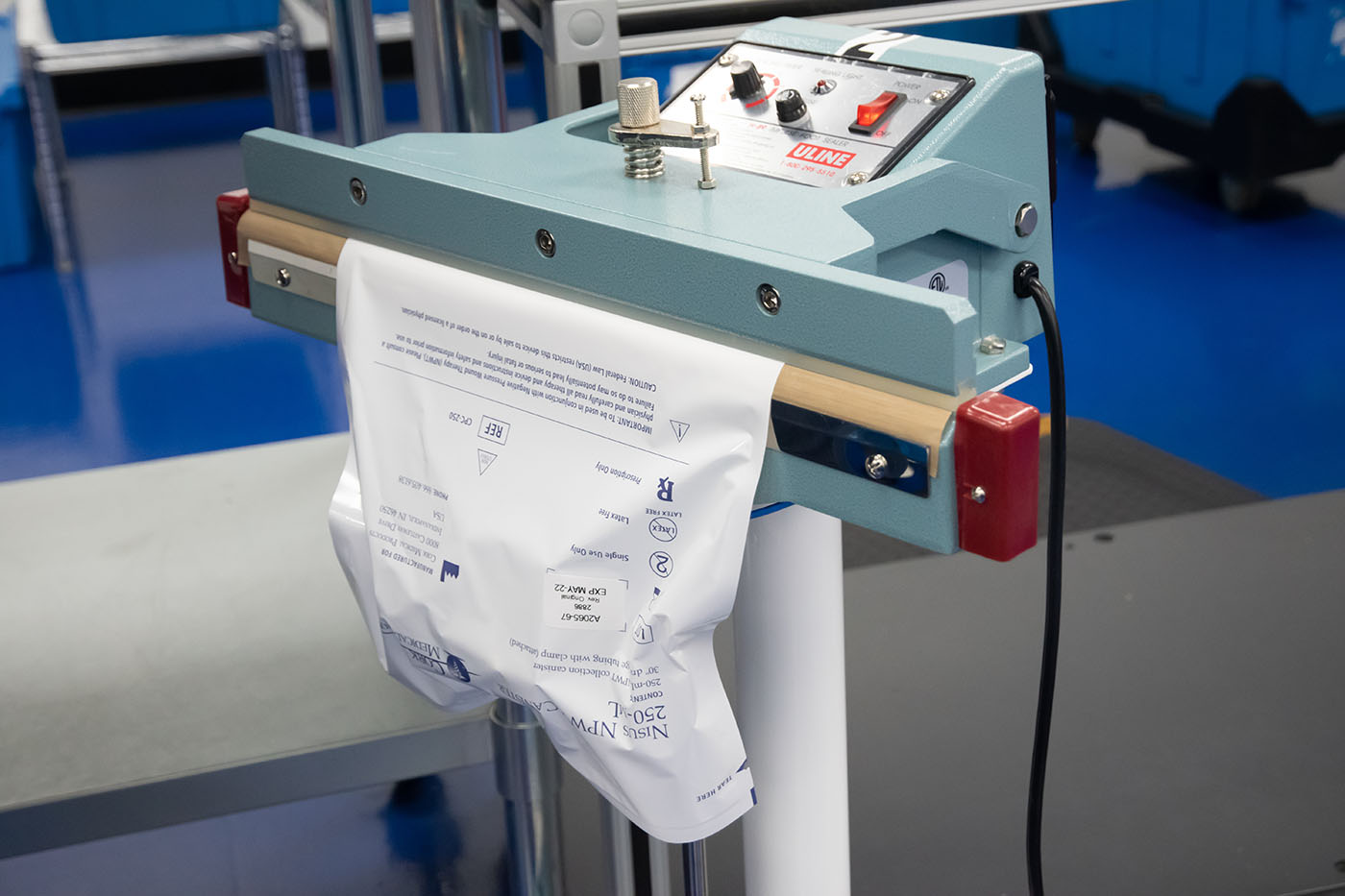
We’ve invested in state-of-the-art ultrasonic welding equipment to best serve your assembly needs. Our equipment is manufactured by the world’s leading plastic welding equipment manufacturer that has been innovating in the industry for many decades. A big part of what we appreciate about their ultrasonic assembly systems is how the tooling and/or application can be quickly changed, thereby offering flexibility and versatility other assembly processes or systems simply can’t match.
The ultrasonic welders also feature high reliability, long life, and consistent, repeatable performance, which helps keep production costs lower for customers. Ultrasonic assembly is now routinely used in a wide range of industries, including the automotive, medical, electrical and electronics, communications, appliance, consumer products, toys, textile, and packaging industries.
Because sonic welding is now such an economical process, our customer clients enjoy how it can significantly increase production while at the same time lowering assembly costs. Our Dukane ultrasonic welders can be easily integrated into our automation-driven manufacturing environment, and the equipment provides unprecedented repeatability, reliability, and accuracy to the process. If the ultrasonic welding capabilities at Global Plastics are of interest to your company, we invite you to get in touch through the contact us page of our website. We look forward to discussing your needs and offering the solutions you require.