Custom Injection Molding
Quality Made Us Global
Custom Injection Molding with Global Plastics
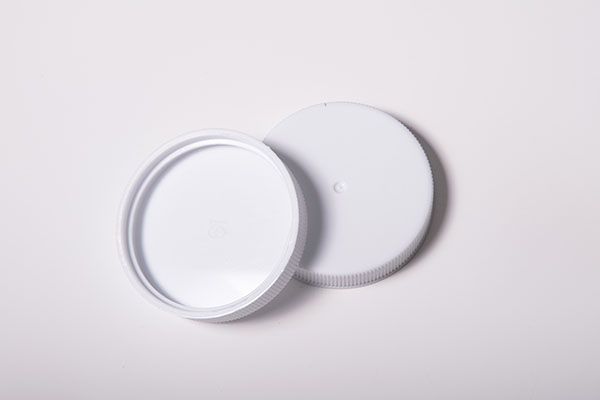
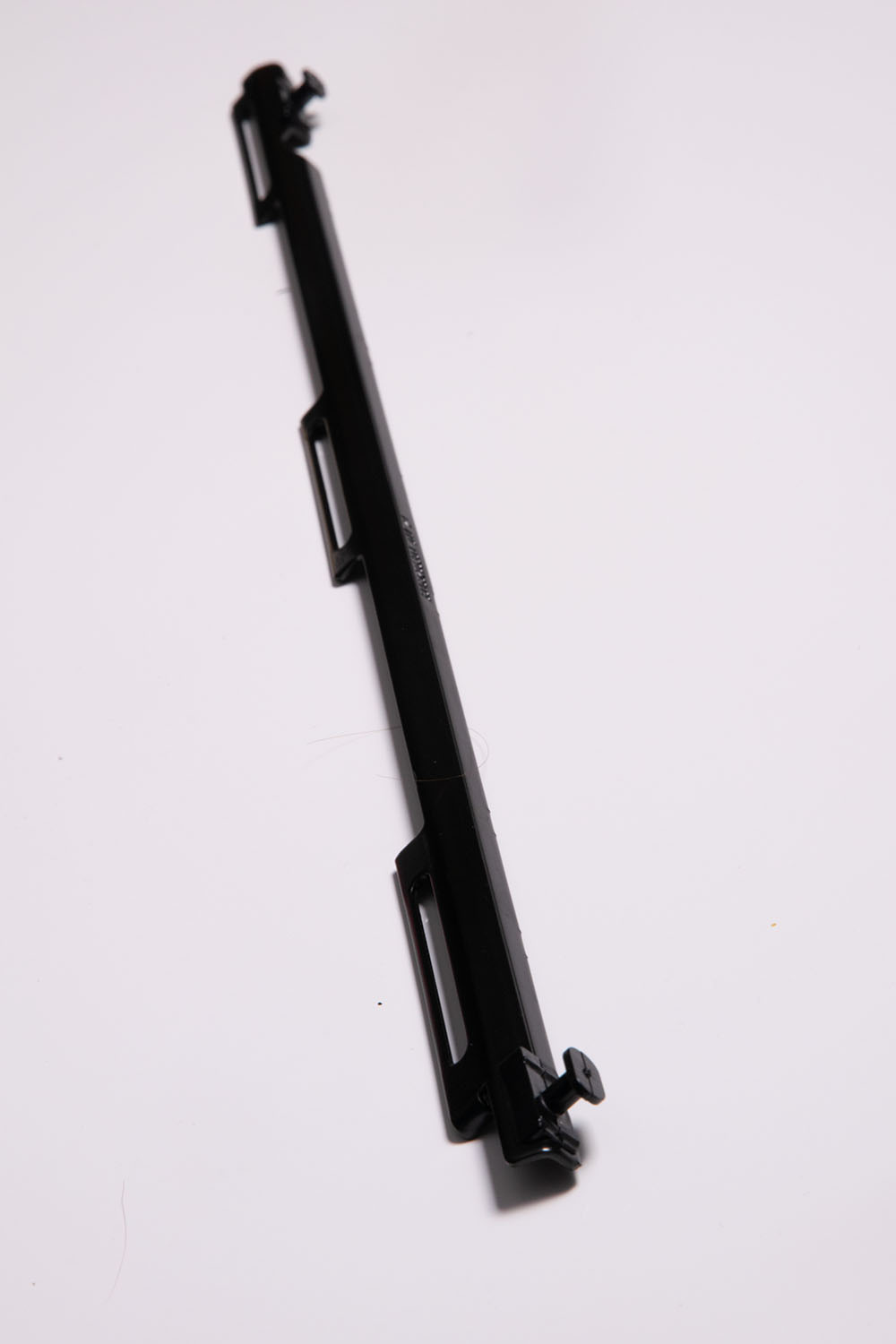
Over the years we’ve had the opportunity to work with customer clients on niche projects to meet specific custom injection molding needs. This has allowed us to develop deep expertise in a wide range of plastic injection molding services other providers lack. You’ll be hard-pressed to find a plastic injection molding partner with the sheer breadth of experience you get with Global Plastics.
Your Vision Combined with Our Expertise and Innovation
During the decades that have passed since our founding in 1992, Global Plastics has made a huge variety of injection molded parts and components. Whatever it is you’re envisioning, chances are good that we can make it. We work with you in close collaboration to turn your vision into the plastic injection molded pieces you need. Below are some examples of our wide-ranging experience.
Global Plastics makes hundreds of thousands of plastic injection molded components every year for use in the HVAC industry, and we’ve been doing that for many years. In many cases, these are components that would otherwise have to be made from much more expensive steel. The challenge is in identifying and using the right plastic materials that can resist the corrosion so prevalent in HVAC equipment.
Thanks to the huge variety of high-performance plastic resins available today as well as long-fiber compounds, industrial gears made of plastic have come a long way. High-quality, durable, precision plastic gears can be produced through the injection molding process for a wide range of demanding applications. Complex part geometry, high-performance specifications, and larger sizes are now possible with Global Plastics because of the expertise, equipment, and materials we have at our fingertips. The key to precision gears is in the process controls that allow for higher accuracy and a tighter window across a range of variables in order to not only meet but in many cases to exceed your requirements.
In the world of electronics, every circuit board needs to be contained and protected by a plastic “box” or enclosure of some kind. The possibilities here are nearly endless, including cases for handheld electronic devices, NEMA 4 cases, pocket box enclosures, mobile box enclosures, taper end enclosures, shell cases, desktop enclosures, LCD cases (including angled cases, sloped bottom cases, etc.), instrument cases, precision miniature cases, flange and wall mount cases, open front enclosures, and pretty much any other permutation you can dream up.
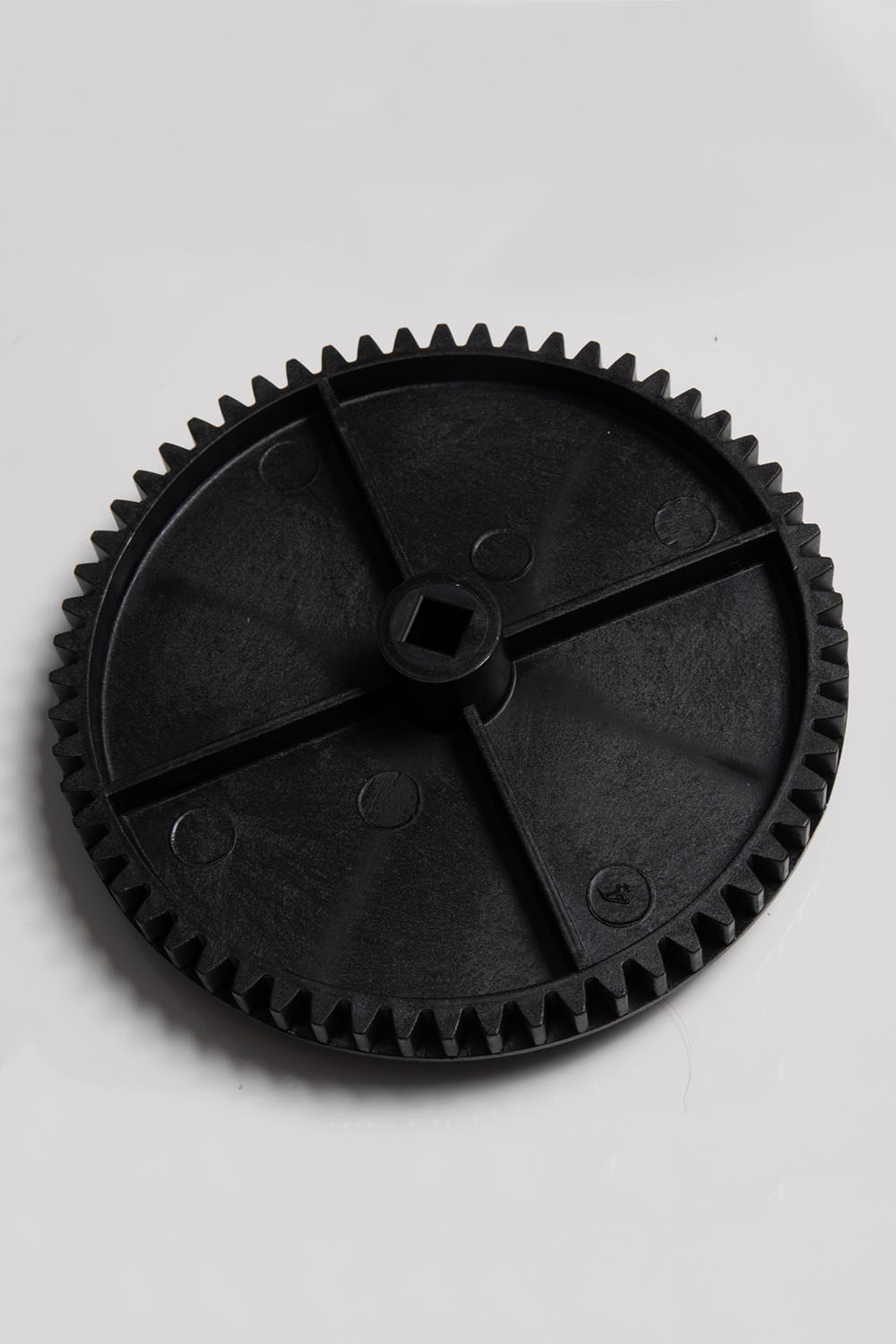
A highly engineered plastic part is going to be much lighter in weight than its metal predecessor, as well as more flexible for better performance and functionality. Is metal to plastic conversion feasible for what you have in mind? The design engineers at Global Plastics can help you determine this with a feasibility study that examines three essential factors: design, manufacturability, and return on investment. After all, the point of metal to plastic conversion projects is to gain a variety of benefits, including efficiencies in cost, performance, weight, durability, and aesthetics.
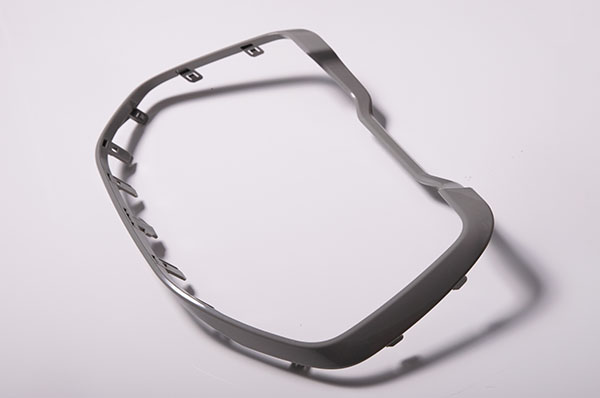
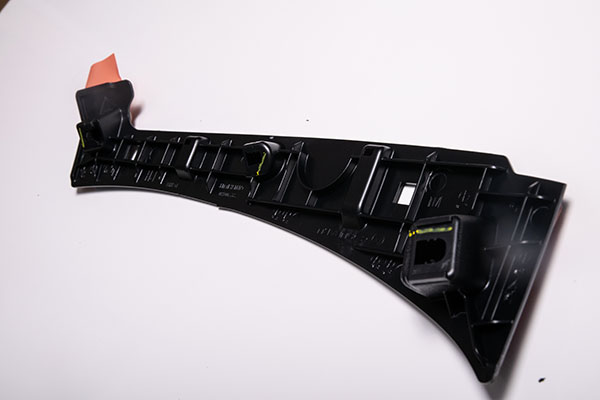
Although it sounds cliché, it really is true that if you can think it, more than likely we can make it. Whatever it is you want to accomplish, we can help you quickly determine whether plastic injection molding is the right approach for producing your vision. The technological advances that have occurred plastic injection molding lets you think outside the box to discover what’s possible with plastic.
While it may be tempting to go with a low-price plastic injection molding provider, they don’t offer the full range of expertise or provide adequate control over the total delivered cost (TDC) to take your project from initial concept to ongoing production runs and beyond. Global Plastics a full-service injection molding partner who manages your project through the entire life cycle. With a full-service, in-house tooling department and a wide range of value-added services, we serve as a one-stop solution for all the plastic injection molding services you’ll ever need. We look forward to hearing from you through the contact us page of our website to discuss your needs and how we can meet them.
Global Plastics has Safe Quality Food (SQF) certification for manufacturing food packaging materials and plastic molded food closures.